What Affects Lead Times in Job Shop Manufacturing?
Leave a Comment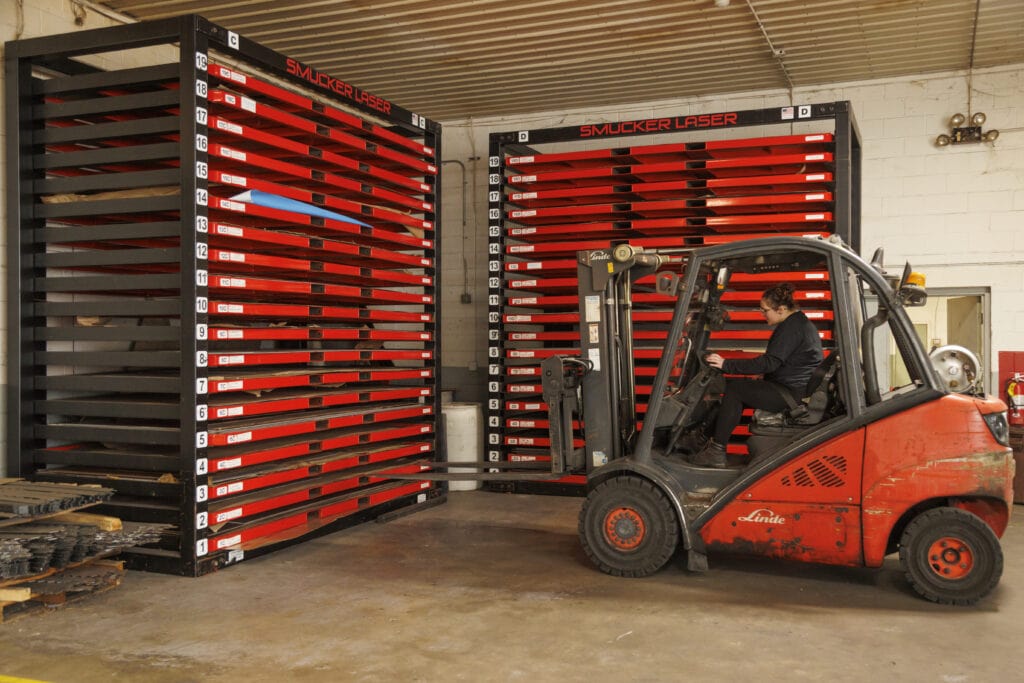
When it comes to job shop manufacturing, one of the most common questions we get asked is, “How long does it take to complete a project?” A close second is, “What factors affect lead times?” Understanding the answers to these questions is important for anyone in need of custom manufacturing services or those seeking to improve their own processes. In this blog, we’ll explore the key factors that influence manufacturing lead times and share insights on how to manage them effectively.
What Are Lead Times in Job Shop Manufacturing?
Lead time is the total time it takes to complete a manufacturing project from the moment an order is placed to when the finished product is delivered. In job shop manufacturing, where custom orders and small batch production are the norm, lead times can vary significantly depending on several variables. For businesses relying on timely production, understanding these variables is key to maintaining efficiency and meeting customer expectations.
Key Factors That Affect Lead Times
1. Supplier Reliability
The dependability of your suppliers plays a critical role in determining lead times. If a supplier consistently delivers raw materials late or provides subpar quality materials, production can come to a halt. Building relationships with reliable suppliers and determining consistent delivery schedules can help mitigate this risk. Additionally, sourcing from multiple suppliers reduces the risk of delays from a single source.
2. Raw Material Availability
Limited availability of raw materials is a common bottleneck. When specific metals or alloys are in high demand, lead times can be extended while waiting for supply. For example, at Smucker Laser Cutting, we use materials like aluminum, stainless steel, and mild steel, and we’ve built systems to ensure stock availability for our most common projects. Monitoring market trends and maintaining strategic inventory levels can help reduce the impact of raw material shortages.
3. Job Complexity
The complexity of a job, including design intricacy and the number of manufacturing steps, directly affects processing time. Projects requiring intricate laser cutting or multiple fabrication processes will naturally take longer to complete than simpler jobs. Clear communication of project requirements during the design phase can help streamline production. Collaborating with clients on design optimization to identify potential simplifications can maintain quality while reducing production time.
4. Machine Downtime
Unexpected equipment breakdowns can severely impact production schedules. Preventative maintenance is essential to reduce the likelihood of machine downtime. Our laser machines are regularly serviced to ensure they operate efficiently and consistently. Investing in backup equipment or having contingency plans in place can further mitigate the risks associated with machine failures.
5. Production Scheduling
Inefficient scheduling practices can lead to extended lead times, particularly if urgent orders are not prioritized or if there is an over-reliance on manual scheduling methods. Advanced scheduling software can optimize job sequencing to improve turnaround times. At Smucker Laser Cutting, we leverage technology to create balanced production schedules that maximize throughput and minimize delays.
6. Labor Availability
Staff shortages or skill gaps can create bottlenecks in production. Cross-training employees to handle multiple tasks and investing in workforce development can significantly reduce delays caused by labor limitations. A skilled and flexible workforce is especially crucial in job shop manufacturing, where project requirements can vary widely.
7. Quality Control and Inspection
High-quality standards often require extensive inspection procedures. While necessary to ensure product integrity, these additional steps can add time to the production cycle. At Smucker Laser Cutting, we balance thorough quality checks with efficient workflows to minimize delays without compromising standards. Implementing in-line inspection systems or statistical process controls can further enhance quality without adding excessive time to the process.
8. Customer Order Variability
Frequent changes in customer orders, such as modifications to design specifications or quantities, can disrupt production flow and increase lead times. Clear communication and setting realistic expectations upfront can help manage these changes. Providing clients with detailed project timelines and revision policies can also help minimize disruptions.
9. Transportation Logistics
Delays in shipping finished products to customers can extend overall lead times. Partnering with reliable logistics providers and maintaining clear communication throughout the delivery process is critical. For regional projects, consider using local delivery services to reduce transportation time. Additionally, tracking shipments in real-time can provide customers with updates and improve satisfaction.
How We Manage and Reduce Lead Times
While some factors influencing lead times are outside of our control, there are several strategies we use to manage and reduce delays:
Develop Strong Supplier Relationships:
Work with dependable suppliers and maintain open communication to ensure timely delivery of raw materials.
Maintain Effective Inventory Management:
Keep sufficient stock of essential materials to avoid shortages that could halt production.
Implement Preventative Maintenance:
Regularly inspect and service machinery to prevent unexpected breakdowns.
Streamline Production Processes:
Identify and eliminate inefficiencies in your workflow to reduce unnecessary steps and waiting times.
Utilize Advanced Scheduling Tools:
Leverage software solutions to optimize production schedules and prioritize urgent jobs.
Invest in Workforce Flexibility:
Cross-train employees to handle various tasks and minimize disruptions caused by labor shortages.
Set Clear Customer Expectations:
Provide realistic timelines and communicate any changes promptly to avoid last-minute surprises.
Optimize Workflow Layout
Analyze shop floor layout to reduce unnecessary movement of materials and improve overall efficiency.
Adopt Lean Manufacturing Principles:
Implement lean manufacturing techniques to minimize waste and enhance production flow.
Why Choose Smucker Laser Cutting for Your Manufacturing Needs?
At Smucker Laser Cutting and Metal Fabrication, we understand the importance of timely project completion. Our state-of-the-art laser machines and full line of fabrication equipment enable us to handle everything from prototyping to long production runs efficiently. Additionally, we prioritize effective communication with our customers to ensure smooth workflows and on-time delivery.
We also offer a range of services tailored to meet the diverse needs of industries such as OEMs, military, transportation, and recreational sectors. Visit our services page to explore how we can assist with your next project.
FAQs About Lead Times in Job Shop Manufacturing
How can job shop manufacturers reduce lead times?
Manufacturers can reduce lead times by optimizing production schedules, maintaining strategic inventory levels, and leveraging advanced technologies.
What are the most common causes of delays in custom manufacturing?
Delays often stem from material shortages and machine downtime.
How does lean manufacturing improve lead times?
Lean manufacturing minimizes waste and enhances workflow efficiency, reducing unnecessary steps and improving production speed.
Partner with Us for Precision and Reliability
Understanding the factors that affect lead times in job shop manufacturing can help you plan projects more effectively and choose the right manufacturing partner. Whether you’re dealing with complex designs, tight schedules, or specific material needs, Smucker Laser Cutting has the expertise to deliver high-quality results on time.
Don’t let lead time challenges hold you back. Contact us today to discuss your project needs, or request a quote to get started on turning your ideas into reality. Together, we can streamline your manufacturing process and exceed your expectations.