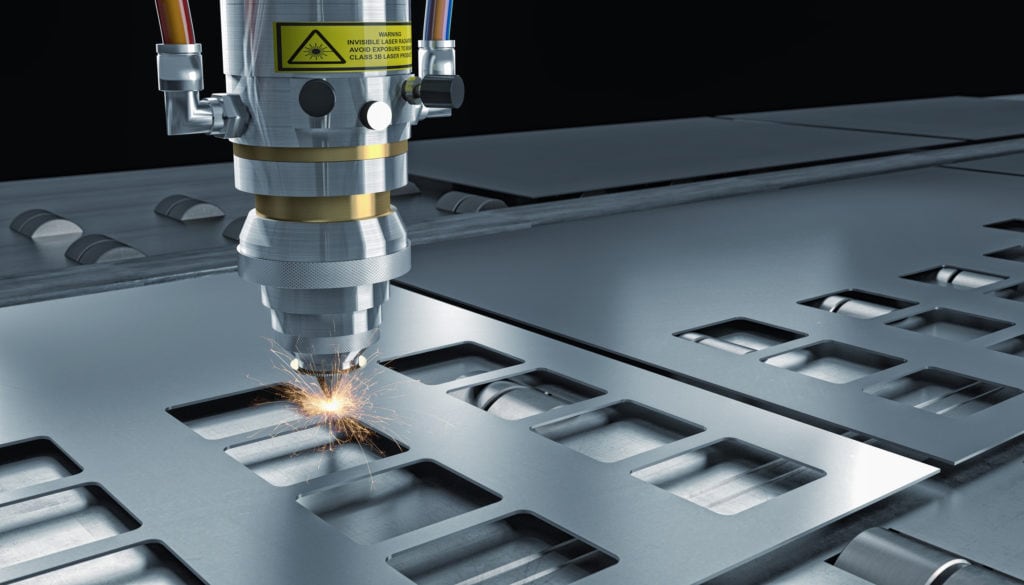
When it comes to laser cutting, selecting the right type of metal for your project is crucial. The choice of material affects everything from the precision of the cut to the durability and appearance of the final product. At Smucker Laser Cutting and Metal Fabrication, we specialize in delivering high-quality laser-cut components for a diverse range of industries, including OEMs, military, transportation, and recreational sectors. In this guide, we’ll walk you through the different types of metals we work with, helping you make an informed decision for your next laser-cut project.
Understanding the Importance of Material Selection
The success of a laser-cut project depends heavily on the material used. Factors such as metal composition, thickness, and properties like strength, malleability, and corrosion resistance play a significant role in determining the final outcome. Whether you’re designing a component for an industrial application or creating a custom part for a new product, choosing the right metal will ensure optimal performance, longevity, and cost-effectiveness.
Common Metals Used in Laser Cutting
At Smucker Laser Cutting and Metal Fabrication, we work with a variety of metals to meet our clients’ specific needs. Below, we explore the characteristics and advantages of some of the most commonly used metals in laser cutting.
1. Aluminum
- Advantages:
- Lightweight and easy to work with
- High strength-to-weight ratio
- Excellent corrosion resistance
- Good thermal and electrical conductivity
- Malleable and can be easily formed into complex shapes
- Applications: Aerospace components, automotive parts, consumer electronics, and architectural elements.
2. Steel
- Advantages:
- High strength and durability
- Cost-effective and widely available
- Can be easily welded and formed
- Available in various grades for specific applications
- Applications: Structural components, automotive parts, heavy machinery, and construction materials.
Types of Steel Options:
1. Mild Steel
- Advantages:
- Cost-effective and easy to weld
- High ductility and malleability
- Can be easily cut, bent, and shaped
- Available in a variety of thicknesses
- Applications: Structural components, automotive parts, machinery, and fabrication projects.
2. Ferrous Metals
- Advantages:
- High strength and hardness
- Cost-effective and widely available
- Magnetic properties in certain alloys
- Suitable for structural and heavy-duty applications
- Applications: Construction, automotive, machinery, and industrial equipment.
3. Heavy Plate
- Advantages:
- High strength and durability
- Suitable for heavy-duty applications
- Can be cut with precision using advanced laser cutting techniques
- Applications: Structural components, industrial machinery, and heavy equipment.
4. Thin Metal
- Advantages:
- High precision and accuracy
- Suitable for intricate designs and patterns
- Minimal distortion during cutting
- Versatile and easy to work with
- Applications: Electronics, medical devices, decorative elements, and prototypes.
3. Stainless Steel
- Advantages:
- Lightweight and easy to work with
- Superior corrosion resistance
- High tensile strength and durability
- Aesthetic appeal with a shiny finish
- Low maintenance and easy to clean
- Applications: Medical instruments, kitchen appliances, architectural elements, and automotive components.
4. Non-Ferrous Metals
- Advantages:
- Corrosion resistance
- Lightweight and easy to work with
- High conductivity (in metals like copper)
- Non-magnetic properties
- Applications: Electrical components, decorative elements, and lightweight structures.
Types of Non-Ferrous Metals:
1. Copper
- Advantages:
- High electrical and thermal conductivity
- Excellent corrosion resistance
- Aesthetic appeal with a unique color
- Easy to form and shape
- Applications: Electrical components, decorative elements, plumbing, and HVAC systems.
2. Brass
- Advantages:
- Aesthetic appeal with a gold-like finish
- Corrosion resistance
- Low friction properties
- Easy to machine and fabricate
- Applications: Decorative hardware, musical instruments, plumbing fixtures, and electrical connectors.
Why Choose Smucker Laser Cutting and Metal Fabrication?
Selecting the best type of metal for your laser-cut project is essential for achieving the desired performance, durability, and appearance. By understanding the properties and advantages of different metals, you can make an informed decision that aligns with your project goals. At Smucker Laser Cutting and Metal Fabrication, we’re here to help you every step of the way, from material selection to final production.
Contact us today to learn more about how our laser-cutting services can benefit your next project, or request a quote to get started.